Machinery Safety Management
Machinery Safety Solutions by BEIMCO
Our Machine Safety services are designed to help industrial facilities comply with international safety standards such as ISO 12100, ISO 13849-1, and IEC 62061, ensuring that machinery operates with minimal risk to personnel and equipment. We provide comprehensive solutions across the entire safety lifecycle—from hazard identification to system architecture design and performance level validation. Whether you’re designing new machinery or upgrading existing systems, we guide you through the complex process of risk assessment and functional safety implementation. Our approach focuses on reducing risk to acceptable levels while maintaining productivity and operational efficiency.
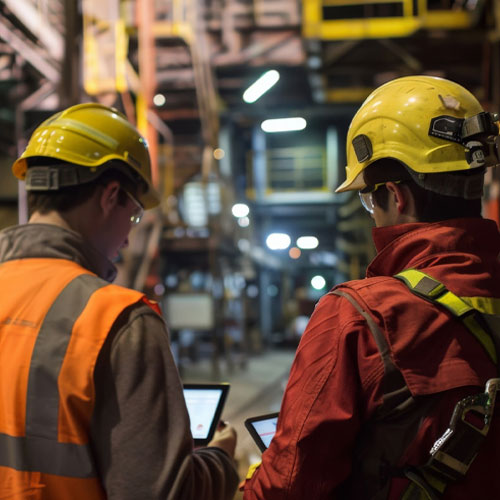
Protecting your workforce with BEIMCO’s smart safety solutions
From assessment to implementation — we secure your machinery operations
Protecting your workforce with BEIMCO’s smart safety solutions
From assessment to implementation — we secure your machinery operations
BEIMCO Machinery Risk & Safety Solutions
Machinery Hazard Identification
Machinery hazard identification is the first and most critical step in the safety lifecycle. Our team conducts thorough evaluations of your machinery and its operational environment to identify all potential hazards. These include mechanical, electrical, thermal, and operational hazards that could pose a threat to personnel or the equipment itself. Using methodologies aligned with ISO 12100, we examine all phases of machine operation, including startup, normal use, maintenance, and emergency stops. The goal is to develop a complete hazard list to serve as the foundation for later risk assessments. We also help you identify hidden and less obvious risks that may not be apparent during basic inspections, ensuring that no safety gaps are overlooked.
Risk Estimation
Once hazards have been identified, we perform detailed Risk Estimation to quantify the severity, frequency, and possibility of avoiding the identified risks. This process helps determine the actual level of risk associated with each hazard and sets the stage for selecting appropriate risk reduction measures. Our risk estimation process aligns with both ISO 12100 and ISO 13849-1, ensuring a systematic and compliant approach. By using structured tools such as risk graphs or tables, we categorize risks into actionable levels that inform the necessary control strategies. This process ensures safety measures are both effective and proportionate to the actual risk, minimizing overdesign while maintaining full compliance.
Determination of Required Performance Level (PLr)
In this phase, we determine the Required Performance Level (PLr) or SIL (Safety Integrity Level) for each safety function, depending on whether you follow ISO 13849-1 or IEC 62061. This involves translating the risk estimation outcomes into a performance requirement that your safety system must meet. The PLr guides the design and implementation of safety-related control functions, such as emergency stops or interlocking devices. Our experts ensure accurate PLr determination by analyzing risk parameters including severity, frequency, and the possibility of hazard avoidance. This ensures that the designed safety functions are robust enough to handle the expected operational risk and achieve legal compliance.
Safety Function Architecture Design
Once the PLr is known, we assist in designing the architecture of safety functions in accordance with ISO 13849-1 or IEC 62061. This includes selecting suitable components, defining safety chains, and establishing redundancy and diagnostic coverage as required. Whether you need a Category 3 or Category 4 architecture, we design control systems that ensure functionality, fault tolerance, and compliance with the required safety level. Our designs take into account practical aspects like wiring, environmental conditions, and existing control systems. We aim to balance safety with simplicity and maintainability, reducing complexity while ensuring a high level of protection for operators and assets.
Performance Level Verification
After implementation, we perform Performance Level Verification (PL verification) to confirm that the safety functions meet the required PLr. This includes quantitative analysis of parameters such as MTTFd (Mean Time to Dangerous Failure), DC (Diagnostic Coverage), and CCF (Common Cause Failure), in line with ISO 13849-1. Using industry-standard tools and calculations, we provide documentation proving that the designed safety functions fulfill the necessary requirements. This verification step is essential for audits, certifications, and legal compliance. It also ensures that the safety system functions reliably over the long term and that your plant remains protected against critical failure scenarios.